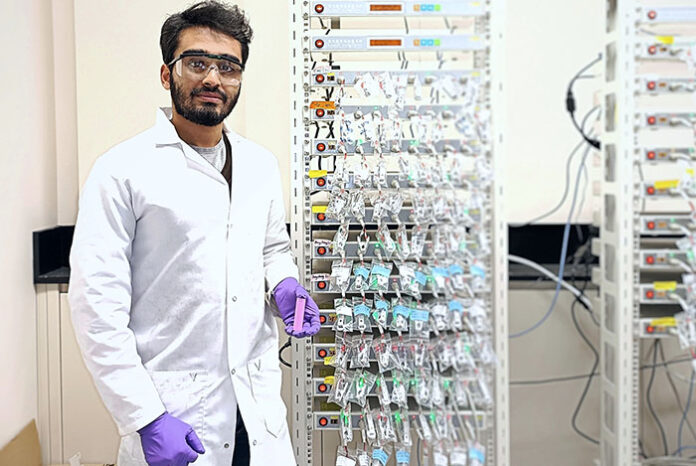
New methods of recovering rare metals from spent batteries could be a win-win for the environment and manufacturers looking to cut costs..
Powering everything from cellphones to electric vehicles, lithium-ion batteries are part of everyday life – but they also wear out eventually, and that comes with a cost to the environment.
Now, a University of Alberta researcher is investigating how to recycle and regenerate used batteries in a more environmentally friendly way.
Anil Kumar Vinayak, a master’s student at the Faculty of Engineering, is experimenting with a method for recycling metals such as lithium and cobalt used in batteries, using circular economy principles as the basis for his work.
Sustainability news:
The idea is based on a circulatory system in which the product and its components are used optimally. Ideal for recycling, reusing, regenerating, upgrading or refurbishing to minimize waste and pollution.
As waste from electrical and electronic equipment has rapidly accumulated over the past decade, “adopting this approach will help solve many of the problems we face in waste management and the environmental issues that come with it,” Vinayak believes.
The concept is also a “perfect model” for addressing several issues in battery production, including cost and mining dependence on raw material supply, supply chain bottlenecks and energy consumption, he added.
Located in Professor Wang Xiaolei’s laboratory, Vinayak has made an environmentally friendly transformation of hydrometallurgy. This is one of the current ways to recycle the metal from used batteries to reuse them in the manufacture of new batteries.
The process typically uses harsh mineral acids, but to recover the metal from the cathode (the positive electrode of the battery), Vinayak is experimenting with milder organic chemicals with minimal environmental impact.
Less corrosive and toxic chemical mixtures also mean maintenance and disposal cost savings for the industry. Since they can be reused, organic alternatives are more economical for recycling companies operating in niche markets, Vinayak said.
Using a similar approach, he is also working to make the current process for recycling graphite, a mineral used in the negative electrode of batteries, called the anode, more sustainable. After cleaning and repair, the graphite can be reused in new batteries or reprocessed for other uses, such as lubricants.
Vinayak is also continuing previous U-of-A research to see if it can increase battery capacity by “doping” it with nickel and manganese to recover the metal from spent cathodes.
He noted that all work showed promising performance results.
Vinayak has recovered more than 80 percent of the lithium from used batteries using its organic acid blend, and “as that number approaches 100 percent, it can be scaled up to an industrial scale,” he said.
He added that organic acids could be adopted “almost immediately” as the hydrometallurgical process is already widely used.
Vinayak has also achieved complete regeneration of graphite from spent anodes, a step towards greater sustainability.
“It is exciting to obtain results comparable to existing methods through an environmentally friendly alternative.”
Finally, Vinayak thinks it would also be good news to breathe new life into old batteries in a more sustainable way.
“This work benefits battery and automakers, as well as industries that rely on metals commonly found in batteries.
“The impact is fairly relevant and imminent.”
Vinayak’s work was funded by Future Energy Systems, an interdisciplinary research and teaching network at U of A dedicated to innovating for the energy transition.
Source: University of Alberta